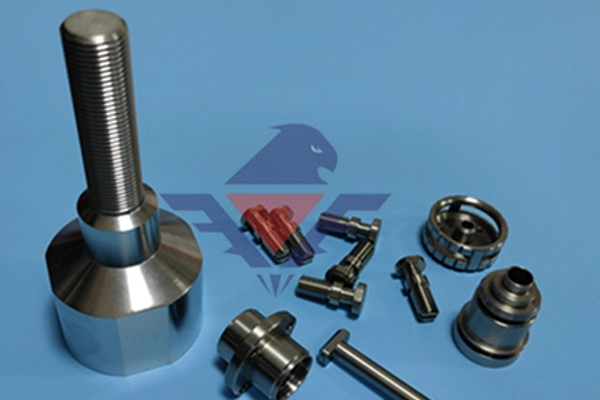
,文章长度约1000词左右。
# Precision Swiss Machining Solutions for Complex Components
## Introduction to Swiss Machining
Swiss machining, also known as Swiss screw machining or Swiss turning, is a specialized manufacturing process that excels in producing high-precision, complex components with tight tolerances. Originating from Switzerland’s watchmaking industry, this advanced machining technique has evolved to serve various industries requiring intricate parts with exceptional accuracy.
The Swiss machining process differs from conventional CNC turning in its unique guide bushing system that provides unparalleled support to the workpiece during cutting operations. This innovative approach allows for the production of slender, complex parts that would be challenging or impossible to manufacture using traditional methods.
Keyword: Swiss Machining
## How Swiss Machining Works
At the heart of Swiss machining lies the sliding headstock and guide bushing system. The workpiece extends through the guide bushing, which remains stationary while the cutting tools move along the Z-axis to perform operations. This setup provides exceptional stability, minimizing deflection even when working with long, slender parts.
Key features of Swiss machining include:
– Simultaneous operations: Multiple tools can work on different sections of the part simultaneously
– Exceptional precision: Capable of maintaining tolerances within ±0.0002 inches
– Reduced vibration: The guide bushing minimizes workpiece movement during cutting
– Efficient material usage: Minimizes waste through precise control
## Advantages of Swiss Machining
### 1. Superior Precision for Complex Geometries
Swiss machining excels at producing components with intricate features such as:
– Micro-sized parts with diameters as small as 0.5mm
– Complex contours and profiles
– Precise threading and grooving
– Multi-diameter shafts with tight concentricity requirements
### 2. Enhanced Efficiency in High-Volume Production
The Swiss machining process offers significant advantages for mass production:
– Reduced setup times through quick-change tooling systems
– Continuous bar feeding for uninterrupted production
– Automated part handling options
– Consistent quality across large production runs
### 3. Material Versatility
Swiss machines can work with a wide range of materials including:
Material Type | Examples
Metals | Stainless steel, titanium, brass, aluminum, copper
Plastics | PEEK, Delrin, PTFE, nylon
Exotic Alloys | Inconel, Hastelloy, Monel
## Applications Across Industries
### Medical Device Manufacturing
The medical industry relies heavily on Swiss machining for critical components:
– Surgical instruments
– Implantable devices
– Dental components
– Diagnostic equipment parts
### Aerospace Components
Swiss machining meets the stringent requirements of aerospace applications:
– Fuel system components
– Actuator parts
– Sensor housings
– Fasteners and fittings
### Electronics and Microtechnology
The precision of Swiss machining is ideal for electronic components:
– Connector pins
– Miniature shafts
– Optical device components
– Micro-switch parts
## Choosing the Right Swiss Machining Partner
When selecting a Swiss machining service provider, consider these critical factors:
### Technical Capabilities
– Machine specifications and tooling options
– Quality control systems
– Material expertise
– Secondary processing capabilities
### Quality Assurance
Look for providers with:
– ISO 9001 or AS9100 certification
– Comprehensive inspection equipment
– Statistical process control methods
– Traceability systems
### Experience and Expertise
Evaluate the provider’s:
– Industry-specific experience
– Engineering support capabilities
– Problem-solving approach
– Track record with similar projects
## Future Trends in Swiss Machining
The Swiss machining industry continues to evolve with several emerging trends:
### 1. Advanced Automation
Integration of robotics and AI for:
– Automated loading/unloading
– In-process inspection
– Predictive maintenance
– Adaptive machining
### 2. Smart Manufacturing
Implementation of Industry 4.0 technologies:
– IoT-enabled machine monitoring
– Digital twin simulations
– Cloud-based data analytics
– Real-time performance optimization
### 3. Hybrid