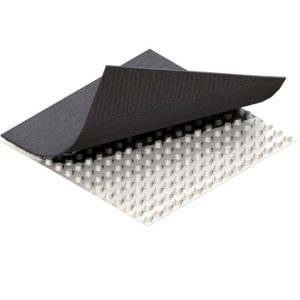
# Optimizing Factory Geotextile Performance for Superior Results
When it comes to construction and civil engineering projects, the quality of materials used can make or break the outcome. Among these materials, factory geotextiles play a crucial role in ensuring stability, durability, and efficiency. To achieve the best results, it’s essential to optimize the performance of factory geotextiles. This article delves into the key factors that contribute to superior geotextile performance and how to leverage them for your projects.
## Understanding Factory Geotextiles
Factory geotextiles are synthetic fabrics used in a variety of civil engineering applications. They are designed to improve soil stability, provide erosion control, and enhance drainage systems. The effectiveness of these geotextiles depends on their material composition, manufacturing process, and proper installation.
### Material Composition
The choice of material is fundamental to the performance of factory geotextiles. Common materials include polypropylene and polyester, each offering unique benefits:
– **Polypropylene**: Known for its excellent chemical resistance and durability, polypropylene is ideal for environments with harsh chemicals or high moisture levels.
– **Polyester**: Offers superior tensile strength and UV resistance, making it suitable for long-term outdoor applications.
### Manufacturing Process
The manufacturing process significantly impacts the quality of factory geotextiles. Advanced techniques such as needle punching and heat bonding ensure that the geotextiles have the necessary strength and permeability. Consistency in manufacturing is key to producing geotextiles that meet industry standards and project requirements.
## Key Factors for Optimizing Performance
To achieve the best results with factory geotextiles, consider the following factors:
### Proper Selection
Selecting the right type of geotextile for your specific application is crucial. Factors to consider include:
– **Soil Type**: Different soils require different geotextile properties. For instance, sandy soils may need geotextiles with higher permeability, while clayey soils may benefit from geotextiles with better filtration capabilities.
– **Load Requirements**: The geotextile must be able to withstand the expected loads without compromising its integrity.
– **Environmental Conditions**: Consider factors such as UV exposure, chemical exposure, and temperature fluctuations when choosing a geotextile.
### Installation Techniques
Proper installation is just as important as selecting the right geotextile. Incorrect installation can lead to reduced performance and even failure. Key installation tips include:
– **Surface Preparation**: Ensure the surface is clean, level, and free of debris before laying the geotextile.
– **Overlap and Seaming**: Properly overlap and seam the geotextile to prevent gaps that could compromise its effectiveness.
– **Anchoring**: Secure the geotextile at the edges and seams to prevent movement during construction and use.
### Maintenance and Monitoring
Regular maintenance and monitoring can extend the lifespan of factory geotextiles and ensure they continue to perform optimally. This includes:
– **Inspections**: Regularly inspect the geotextile for signs of wear, damage, or clogging.
– **Cleaning**: Remove any debris or sediment that may accumulate on the geotextile surface.
– **Repairs**: Promptly repair any damage to prevent further deterioration.
## Conclusion
Optimizing the performance of factory geotextiles is essential for achieving superior results in construction and civil engineering projects. By understanding the material composition, manufacturing process, and key factors such as proper selection, installation techniques, and maintenance, you can ensure that your geotextiles deliver the best possible performance. Investing in high-quality factory geotextiles and following best practices will not only enhance the durability and stability of your projects but also provide long-term cost savings.
Keyword: Factory geotextile best